Key bookkeeping terms in inventory management encompass valuation methods like FIFO, LIFO, and weighted average cost, which directly impact your financial statements. I’ll emphasize that tracking metrics such as Inventory Turnover Ratio (ITR) and Days Inventory Outstanding (DIO) are indispensable for operational efficiency. You’ll need to understand carrying costs, storage expenses, and essential stock level terms like Economic Order Quantity (EOQ) and Reorder Point (ROP). Let’s explore these concepts to strengthen your inventory control system.
Basic Inventory Valuation Methods and Their Impact
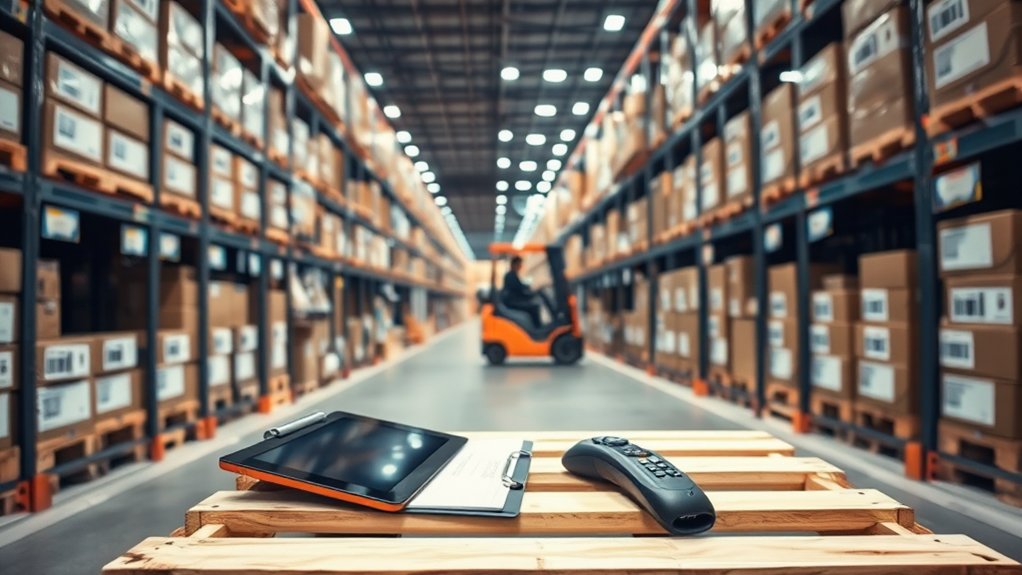
Businesses must choose an appropriate inventory valuation method to accurately track the cost of goods and determine profitability. I’ll outline the three primary methods: FIFO (First-In-First-Out), LIFO (Last-In-First-Out), and weighted average cost.
FIFO assumes older inventory sells first, typically resulting in higher profits during inflation. LIFO counts newest inventory as sold first, often reducing taxable income but potentially understating asset value. The weighted average method calculates a uniform cost per unit across all inventory periods.
Each method impacts your financial statements differently, affecting your tax obligations, profit margins, and balance sheet presentation. Your choice should align with your industry standards and strategic objectives.
Understanding Carrying Costs and Storage Expenses
Beyond tracking inventory values, managing the actual costs of holding stock represents a significant financial consideration. I’ll show you how carrying costs encompass insurance premiums, warehouse utilities, security expenses, and depreciation of stored goods. These expenses directly impact your bottom line.
When I calculate total carrying costs, I factor in both fixed storage expenses like facility leases and variable costs such as labor and handling equipment. Your inventory turnover ratio becomes pivotal here – faster turnover reduces your carrying costs per unit. I recommend monitoring these costs monthly to optimize your storage strategy and maintain competitive pricing.
Essential Inventory Tracking Metrics and Calculations
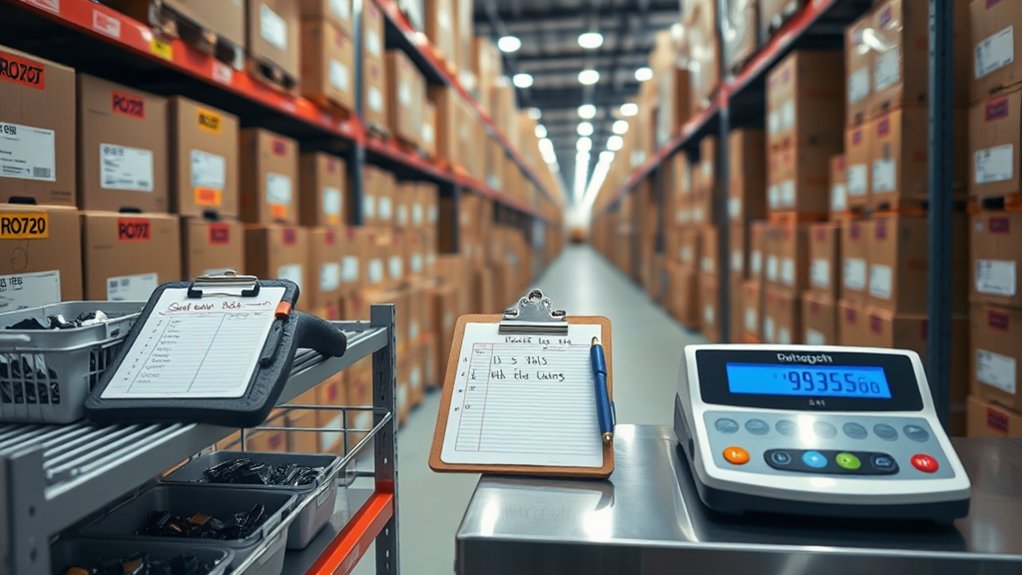
While effective inventory management relies on multiple factors, mastering key performance metrics forms the foundation for data-driven decision making. I recommend focusing on these essential calculations that’ll give you maximum control over your inventory operations:
- Inventory Turnover Ratio (ITR) – Measures how quickly you’re selling and replacing inventory over a specific period
- Economic Order Quantity (EOQ) – Determines the ideal order size to minimize total inventory costs
- Days Inventory Outstanding (DIO) – Calculates the average number of days your inventory remains unsold
I’ve found these metrics consistently deliver actionable insights that enhance operational efficiency and strengthen your market position.
Managing Stock Levels: Key Terms and Formulas
Managing preferred stock levels requires mastering several critical formulas and terminology that form the backbone of inventory control. I’ll guide you through key terms like safety stock, which protects against stockouts, and reorder point (ROP), the level at which you must replenish inventory. Economic Order Quantity (EOQ) helps optimize order sizes by balancing carrying costs against ordering costs. I use Lead Time Demand (LTD) to calculate inventory needed during replenishment periods. These metrics, combined with carrying cost calculations and turnover ratios, empower you to maintain suitable stock levels while minimizing expenses.
Financial Reporting and Inventory Documentation
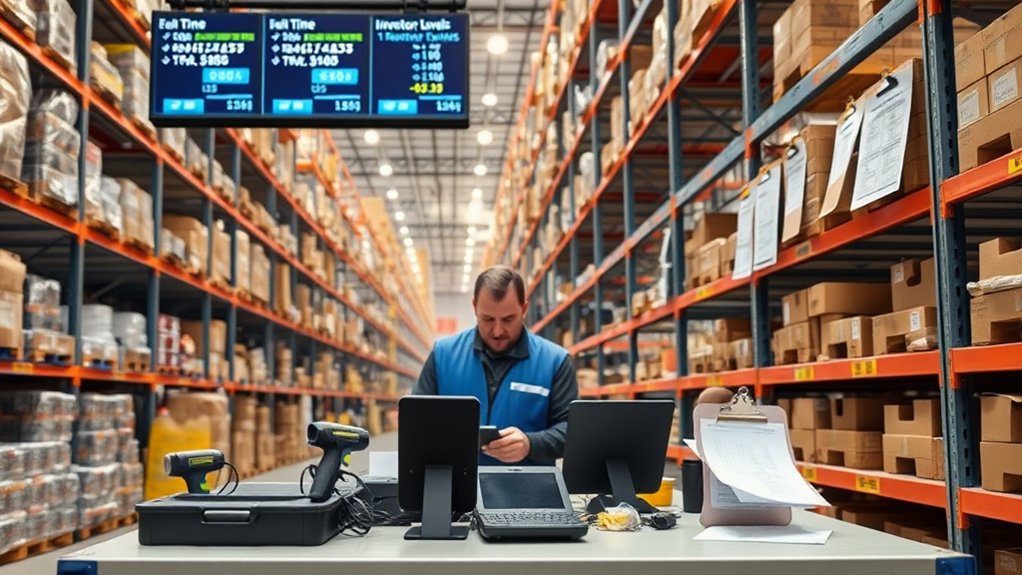
Proper financial reporting sets the foundation for effective inventory documentation and analysis. I recommend mastering these essential reports to maintain control over your inventory assets and make data-driven decisions that impact your bottom line.
- Balance Sheet: Shows your inventory’s current value as an asset, directly affecting your company’s net worth
- Income Statement: Reflects cost of goods sold (COGS) and its impact on profitability
- Inventory Aging Report: Tracks duration of stock holdings, helping identify slow-moving items
Understanding these reports empowers you to optimize inventory levels, reduce carrying costs, and maximize working capital efficiency. Your success depends on accurate documentation and regular analysis.